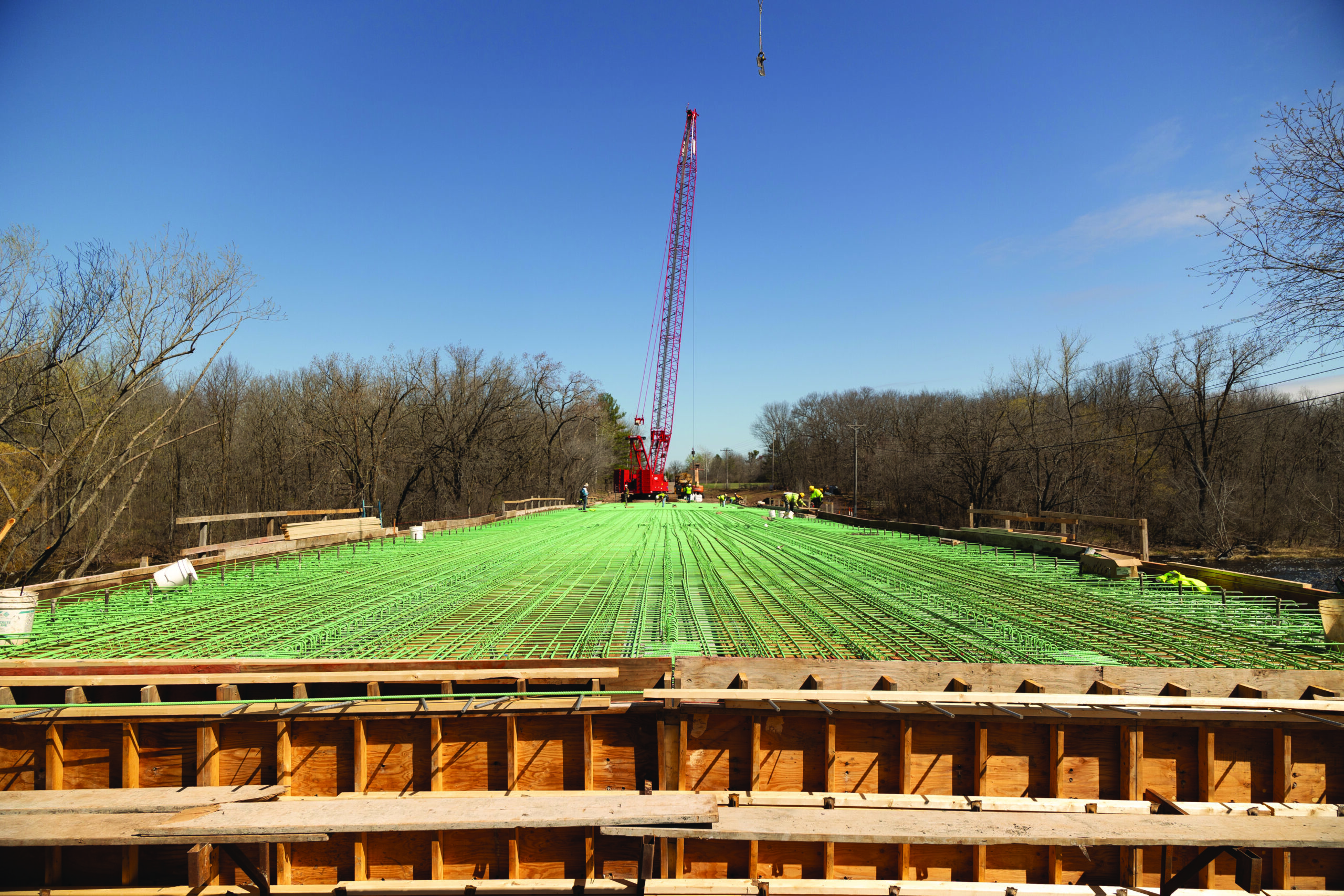
Designing and Improving the Snake River Bridge
August 28, 2024
By Carl Osberg, PE, Director of Structures, WSB
Meeting Traffic Demands and Environmental standards with aesthetic sensitivity
As with many instances of aging infrastructure, the bridge across the Snake River to the East of Pine City, MN reached a point in its lifespan where it needed to be redesigned and replaced. Construction projects like bridges require focused attention to a variety of elements to not only ensure the bridge is sound and long lasting, but also to ensure no concerns are created like blocking off access from boats or environmental concerns. The Snake River Bridge scheduled to be completed in the fall of 2024 provides a superb example of the many facets that make up bridge design.
Meeting Traffic Needs
One point of consideration for bridges are current and future traffic needs. Previously, if farm equipment needed to cross from both sides of the bridge there would be issues. With the newest designs, the addition of extra wide shoulders allows for traffic to flow whether by car or larger. Through traffic forecasting, a bridge design can meet the needs of the current levels of traffic and those estimated for up to 40 years of potential population growth in the area. This project’s analysis deemed additional lanes unnecessary so long as the extra wide shoulders were included. Ensuring the bridge is only as big as is needed will save considerable time and money.
Considering Environmental Data and Concerns
In bridge design, gathering hydraulic data about the river is imperative to ensure that not only will the bridge be able to handle expected seasonal water depths and the speed of the river’s flow, but also to ensure that any bridge design avoids negatively impacting the areas downstream. For example, the updated trail on either side of the bridge included designs for updated drainage ponds and piping to prevent the road and nearby residences from being affected during heavy rains.
When tearing down an existing bridge, care must be taken to ensure that the river is not polluted, and animal habitats are not unnecessarily impacted. Specifically for the Snake River project, remnants of an older bridge still remained and new designs included removal. For both environmental concerns and financial reasons, the Snake River Bridge was designed with the impetus of ensuring durability and expandability. Not only is the bridge made to last, but also if population growth surpasses estimates the bridge can be more easily expanded to fit the new needs rather than torn down and rebuilt again.
To meet environmental and safety concerns, plans for a path underneath the bridge were included in the design that will grant extra protection for drivers, pedestrians, and the local wildlife once the bridge is completed and put to use. Accessible paths allow for foot traffic of both people and animals to maneuver safely without needing to cross the street.
Reducing Costs
Steps were taken through data gathering and design to limit unnecessary costs. These aspects include adding contingencies in relation to the soil and bedrock. Through geotechnical data gathering, it was identified that there are high levels of bedrock close to the surface in the construction area. Building with bedrock is difficult and attention was given to include contingencies on how to handle different bedrock or soil conditions during construction to ensure the project does not stop and cost money and time. Additionally, to limit excess costs geotechnical data was able to be acquired by drilling through the old bridge and into the soil rather than using a barge. Using a barge for data gathering would have drastically increased costs.
A Completed Project With Aesthetic Appeal
Bridge designs like the one used for the Snake River Bridge meet the needs of the communities that use it, protect against environmental impacts to the water, soil and local animals, reduce costs, and provide a timetable to ensure the bridge will be constructed and reopened without delay. Even down to forgoing the usual plain rectangular shapes and including parabolic arches to for little additional funds to make the bridge more attractive and not stand out so much against the beautiful environment around it. Creating not only a finished usable bridge, but one that is attentive to the various needs of the community, the land it sits on, and the river it crosses are what bridge design is all about.
Carl is Director of Structures, and he brings a deep comprehension of MnDOT’s guidelines and protocols for bridge and transportation projects. His extensive experience includes leading studies, engaging with the public and stakeholders, assessing environmental impacts, and overseeing both preliminary and final design stages. Carl has a track record of designing over 70 bridges throughout Minnesota, along with a variety of other structures such as retaining walls, noise barriers, tunnels, and sign structures. His profound knowledge and proven expertise in structural design make him an essential leader, adept at guiding decisive actions and advancing significant projects.
[email protected] | 612.219.3524
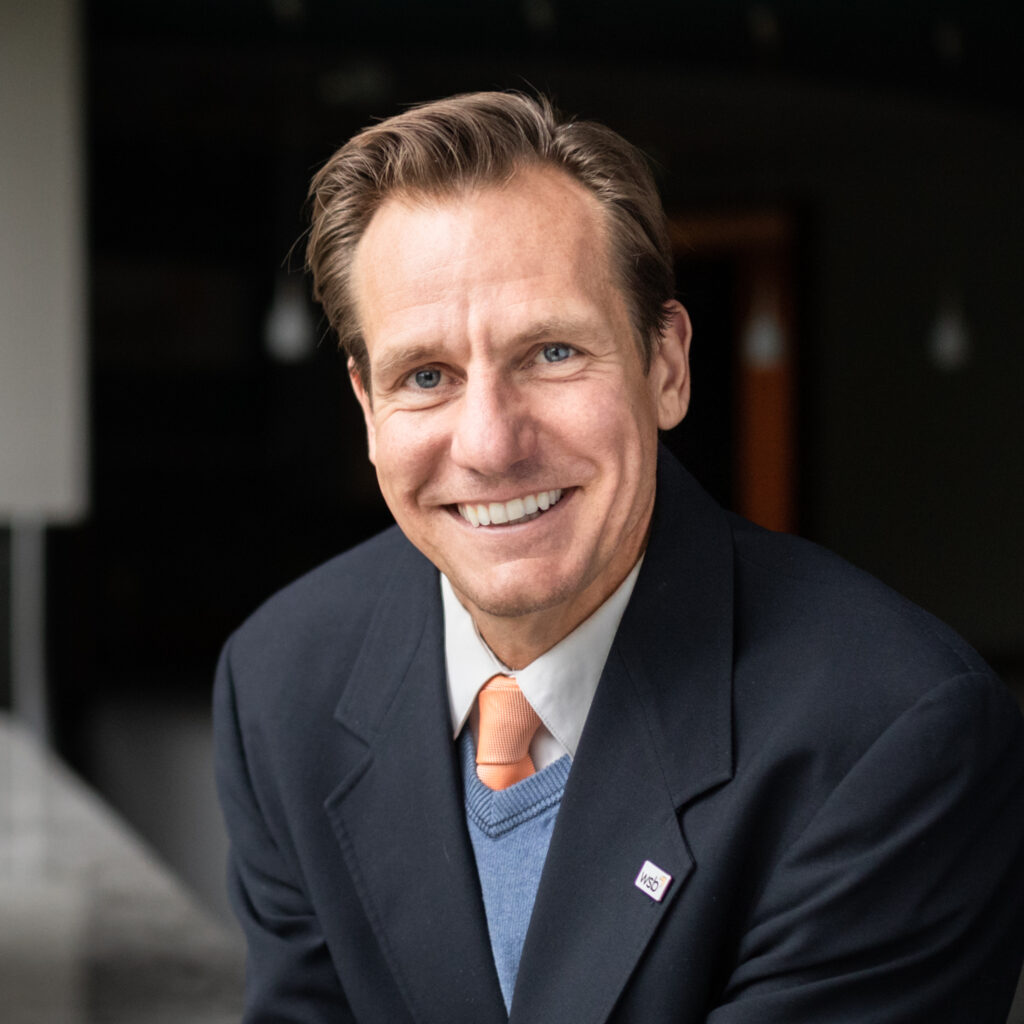