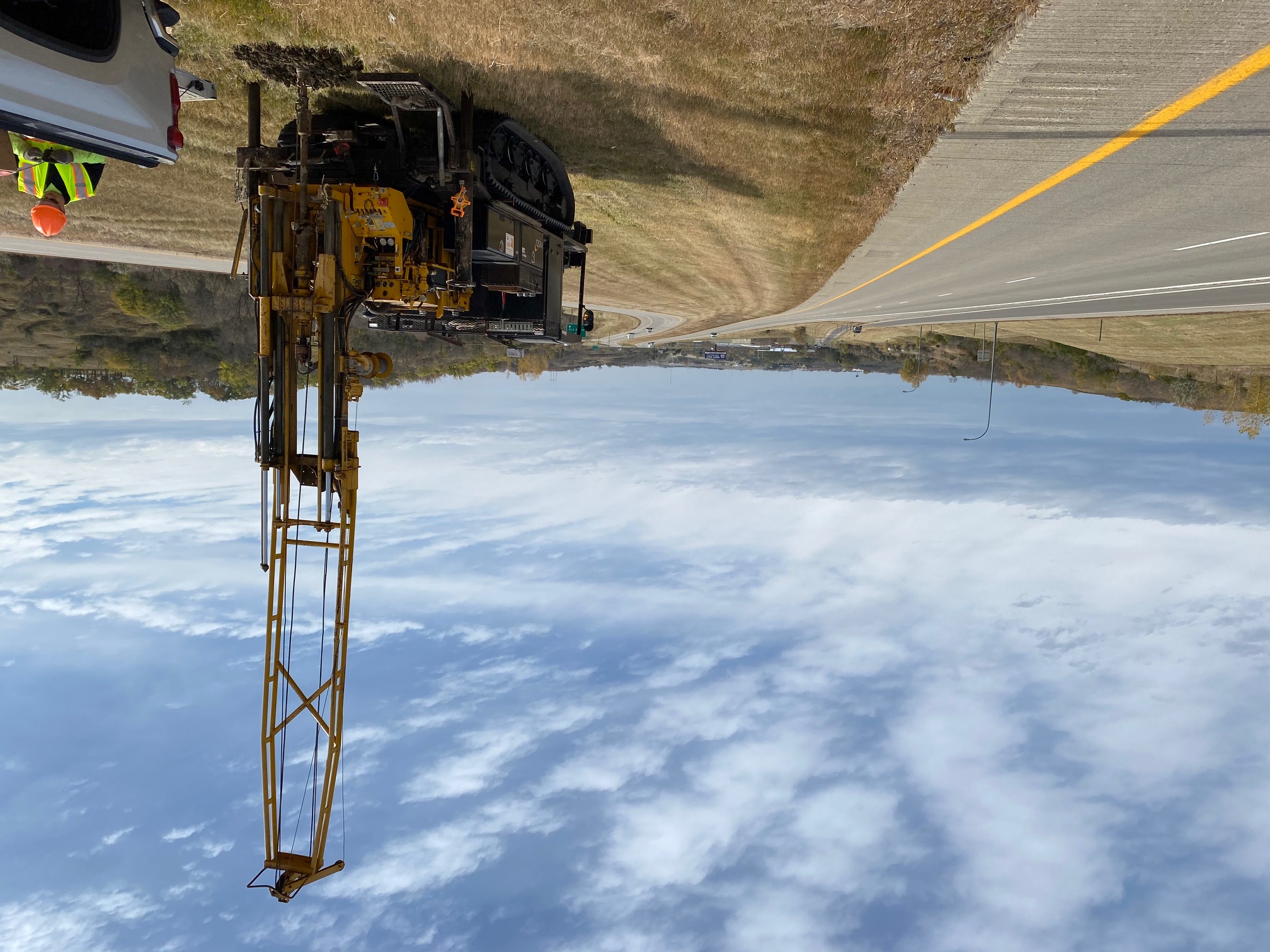
Geotechnical Survey: Three Issues it Can Mitigate in Your Project
June 7, 2024
By Richard Zamora, PE, Director of Geotechnical Services, and Zack Munstermann, PE, Geotechnical Engineer, WSB
A geotechnical survey is a necessity for any construction project to gain an in-depth understanding of underlying soil conditions in order to mitigate costly issues that, if not properly addressed, could damage foundations, walls, pavements and utilities. A good geotechnical survey provides the necessary information like soil strength, depth to bedrock, groundwater levels or slope stability. Knowing what to look for and what to address will improve a project’s design, construction efforts and operations over time. With that in mind, here are a few of the top issues a good geotechnical survey can help to identify and mitigate in your project.
Depth to Bedrock and Related Costs
A geotechnical survey is necessary to understand subsurface conditions and how they will impact a project’s earthwork, structural stability, and costs. Depth to bedrock can heavily influence cost and foundational stability. For instance, if a structure is not designed and built with consideration to bedrock depth, excavation costs could increase and the foundations and walls may experience damage over time requiring future repair work. Shallow depth bedrock is often a benefit for stability and lower project costs. On the other hand, deep layers of bedrock could cause foundational stability issues and will require far more excavation, or a redesign of the foundation leading to higher project costs. What is present in the ground beneath a construction project will dictate potential long-lasting issues that require attention like recurring damages and sinking foundations.
Clay Swelling and Chemical Treatments
Swelling clay, if not properly treated, will drastically increase the risk of structural damage and the need for costly repairs over time. Clay acts like a sponge that cyclically absorbs water and swells before drying and shrinking. After clay soil is properly evaluated through a geotechnical survey and testing, the soil needs to be treated. A survey identifies how much the clay could potentially swell or shrink over time, in order to right-size the treatment plan and not waste valuable resources on excessive excavation, or other costly mitigation measures. One common solution is a moisture treatment, where moisture is mixed into the clay during mass excavation and forced to swell; then, the pre-swelled soil under the foundation is replaced. This ensures swelling does not affect the building.
Chemical treatments are another way to stabilize clay. For shallower structures and pavements, lime and cement can be used and requires less excavation. However, the potential for chemical treatments is also dependent on the presence of sulfates. Sulfates in the soil will react negatively to lime or concrete and worsen the subgrade support. The geotechnical survey will not only help determine whether clay swelling is a problem, but also what treatment is feasible to limit risk and costs.
Presence and Impacts of Groundwater
In addition to soil conditions, a geotechnical survey will identify the potentially detrimental threat of groundwater. Understanding where groundwater is present in the site strata is important, particularly for those structures that have a basement or subsurface utilities. A geotechnical survey can determine groundwater depth at various locations within a construction site. Groundwater can complicate excavations, increase the lateral pressures applied to structures and foundations causing deterioration, and can destroy underground utilities. Proper identification presents the opportunity to develop a subsurface drainage system, or other mitigation alternatives, to keep below-grade utilities, structures, or retaining walls safe. Without a geotechnical survey, the threat posed by groundwater may go unnoticed or be underestimated until it is too late.
How WSB Can Help
At WSB, our Geotechnical team has decades of experience working on projects across the U.S. WSB is prepared to adapt to the needs of local municipalities and to local geology no matter where in the country a project may be. With a highly trained team of experts, clients can expect prepared solutions that mitigate risk and ensure a project’s success.
Richard has over 32 years of experience in the transportation industry of which over 24 years were with the Colorado Department of Transportation. He held various positions throughout his time with the CDOT and a majority of his roles related to pavement and materials including state pavement design and pavement management engineer. In his time at CDOT he implemented pavement design standards, materials quality assurance specifications, and managed the region’s pavement management program.
[email protected] | 719.266.3900

Zack has over 17 years of experience in the Geotechnical profession across multiple states and various levels. Prior to joining WSB, Zack was a project manager and staff engineer coordinating with his team to conduct subsurface explorations, laboratory testing, and preparing geotechnical reports with recommendations for a vast array of projects.
[email protected] | 719.266.3900
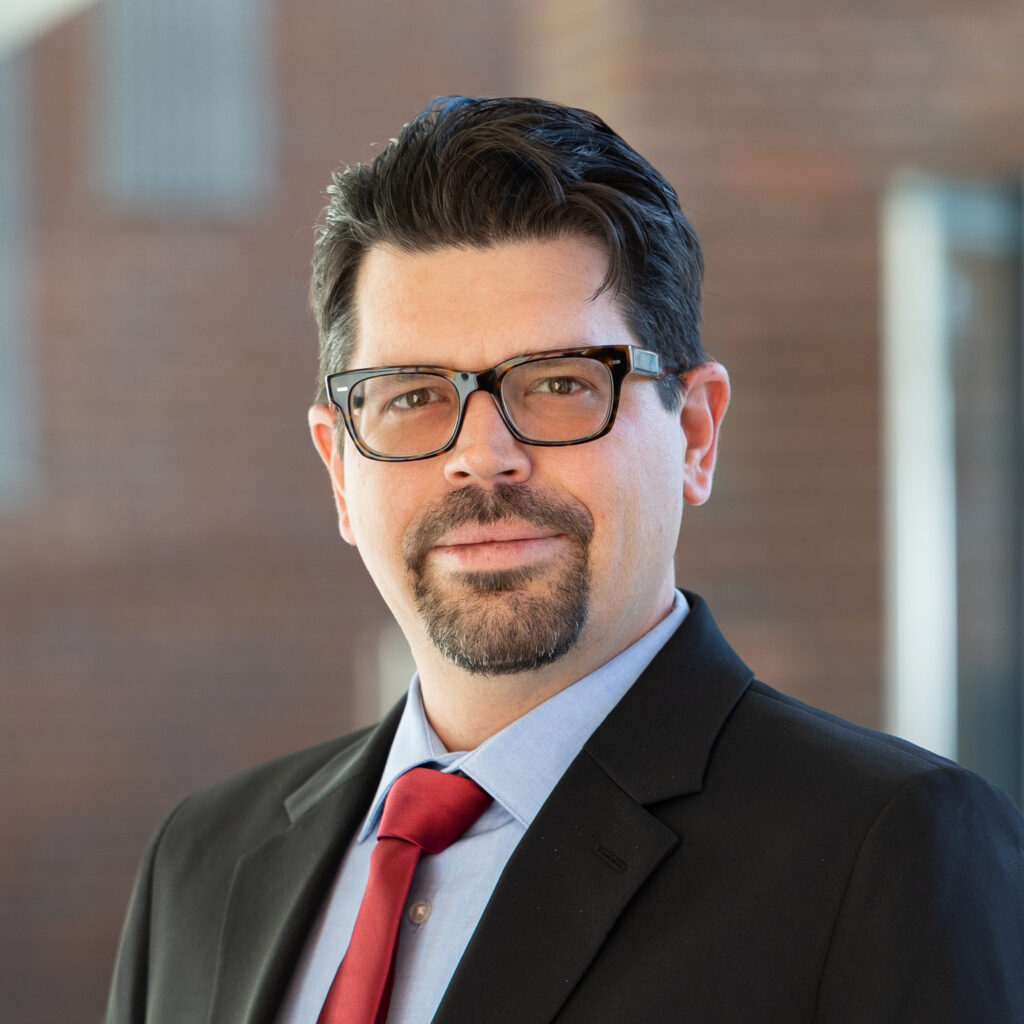